サマリー
ブラザー工業株式会社では、同じ部品倉庫の業務でも生産拠点ごとに異なるシステム・運用を行っていることに課題を抱えていました。特に海外の生産拠点では、急な増産等で大量の部品が入庫される際、適切な保管場所が確保しきれず一時的に通路に置かなければならないなどの問題が発生。結果的に在庫状況が判断しにくくなり、管理の難しさから人員増加によるコスト増に繋がっていました。これらの問題解決のため、「在庫の見える化・部品倉庫作業の効率化・倉庫の面積有効活用」を目的に、統一化された独自の倉庫管理システムを開発。現場スタッフが倉庫内でもシステムを活用するための専用スマートフォンアプリ(以下アプリ)の開発とインフラ整備も同時に実施しました。
プロジェクトの課題
- Excel管理や独自システム導入など国内外の生産拠点ごとに運用方法が異なっており、諸問題の解決と総合的な導入コストを抑えるため、事業を超えた管理システムの統一化を図る必要があった。
- 倉庫の面積有効活用・部品倉庫作業の効率化を実現するため、部品特性・数量に応じてシステム側が自動で倉庫内の物を置く場所を判断・指示できる仕組みを講じる必要があった。
- 並行して、現場スタッフが倉庫内で本システムを活用できるようにするため、モバイル端末の選定から社内向け専用スマホアプリの設計・デザイン、管理・運用方法まで一から検討する必要があった。
- セキュリティ担保のため、モバイル端末の使用を「倉庫エリア内でのシステム利用のみ」に制限し、導入に際してもセキュリティを担保したシステム構成やネットワーク環境の整備を行う必要があった。
課題に対峙した
ABSのアイデア
-
プロダクション&サービス
ソリューショングループM.N今回開発したシステムは、小物・少量部品は「固定ロケーション」に、大物・大量部品は「フリーロケーション」など自動的に最善配置を指示するダブルトランザクション方式の倉庫管理に対応いたしました。本システムにより急な増産時であっても常に最適な保管場所を入庫指示できるようになり、出庫時においても在庫の先入れ・先出しと部品の品質状態まで考慮した出庫指示が出せる仕組みを実現。当初の目的である倉庫の面積有効活用と作業効率化を果たすことができました。
-
プロダクション&サービス
ソリューショングループD.M持ち運びの良さとセキュリティの観点、既存のアプリ配信環境を利用できる点からiPhone端末導入を決定。しかし、当時ブラザー工業様ではiPhoneを業務活用するルールが無かったため、インフラチームの協力のもと、数々のセキュリティ上の問題点を段階的にクリアし、導入に漕ぎ着けました。また私自身、モバイル用のアプリ開発は今回が初めてだったため、システム設計と並行して、スタッフが操作に戸惑わないデザインUIを検討していく過程に苦労しましたが、ローンチ後狙い通りの運用が実現できたことに達成感を感じました。
-
インフラソリューショングループR.T
これまでアクセス制限のない中でのiPhone端末の監視・管理業務の実績はありましたが、今回のように制限された環境下でのアプリ管理は、当社でも前例のない挑戦でした。一言に本システムのアプリだけに限定すると言っても、Appleをはじめ様々な通信先と接続しなければ、そもそも端末を制御できないなどの問題もありました。接続すべき場所としない場所を一つひとつ検討し、何度もトライ&エラーをくり返して、ブラザー工業様が安心して活用できるアプリを導入することができました。
-
インフラソリューショングループT.N
本システムの現地導入を進めるにあたり、私はベトナムと中国の生産拠点を回り、現地担当者への運用方法の指導や、現地無線LAN機器のセットアップを行いました。どんなに便利なシステムも、現場にきちんと浸透してはじめて作業効率化が果たせると思いますので、アプリ操作時の細かなニュアンスまで理解いただけるよう丁寧な説明を心がけました。また、当時入社3年目で海外対応を任せていただけた経験は、その後のキャリアにおいても大きな糧となっています。
Column
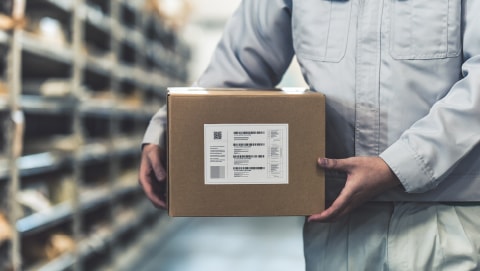
本システムは、部品ごとに保管場所を決める運用方法(固定ロケーション)と、部品を空いている場所に保管する運用方法(フリーロケーション)を併用した倉庫管理システムです。前者は部品を容易に探すことができるメリットがあり、後者は保管場所を効率的に使えるメリットがあります。両者のメリットを生かし、大物・大量部品はパレット単位のフリーロケーション倉庫で、小物・少量部品は固定ロケーション倉庫で管理しています。
プロジェクトの成果
- 2017年より本稼働を開始。プリンター事業、マシナリー事業、工業用ミシン事業のあらゆる事業の国内外生産拠点に導入され、部品倉庫の管理システムの統一化が進んでいる。
- システムの仕組みにより通路にあふれていた在庫は保管場所に収まり、複数人で行っていた入出庫作業も最低限の人員で実現。効率的な部品管理が可能となった。
- 部品の保管場所と持ち出す個数をすぐに把握できるようになった。QRコードの照合により持ち出しミスも軽減し、作業効率が向上。棚卸誤差の軽減、在庫の先入れ・先出しの徹底に繋がっている。
- 今後は本システムで収集したデータにBIツールを活用することで、部品やエリアごとのスタッフ作業効率の分析に役立てるなど、工場の業務改善に繋がる機能提案を検討している。
成果に対する「お客様の声」
-
ブラザー工業株式会社
製造企画部 グループマネジャーH.N様グローバルに展開するブラザーグループの部品倉庫でも、問題解決を円滑に進めることが出来ました。本システムに実装された在庫状況のマップ表示により、現場はもちろん遠く離れた本社からでも即座な状況判断が可能になりました。グループ全体で部品倉庫の業務改革に貢献し、全体のオペレーションの質が向上したことに大変満足しています。今後もアビームシステムズの皆さんには、当社生産拠点の業務プロセス改善を導くようなご提案を期待しています。
プロジェクトの
アーキテクチャ図
-
① システム上で、倉庫に届いた部品の入庫登録を行う。システムは自動で保管場所を提案する。
② 部品情報や保管場所が記載されている指示書が出力され、現場スタッフが部品に貼る。
③ 現場スタッフは指示書通りに部品を保管場所へ格納する。QRコードをアプリで読み取り、保管場所に誤りがないか確認。作業結果を本システムへ記録する。
④ 出庫時には、システムより出庫指示(持ち出す部品や個数)を登録する。
⑤ 現場スタッフがアプリで指示情報を確認し、表示される保管場所へ移動して部品を持ち出す。
部品に貼られた指示書にあるQRコードを照合し、誤りがないか確認。作業結果を本システムへ記録する。
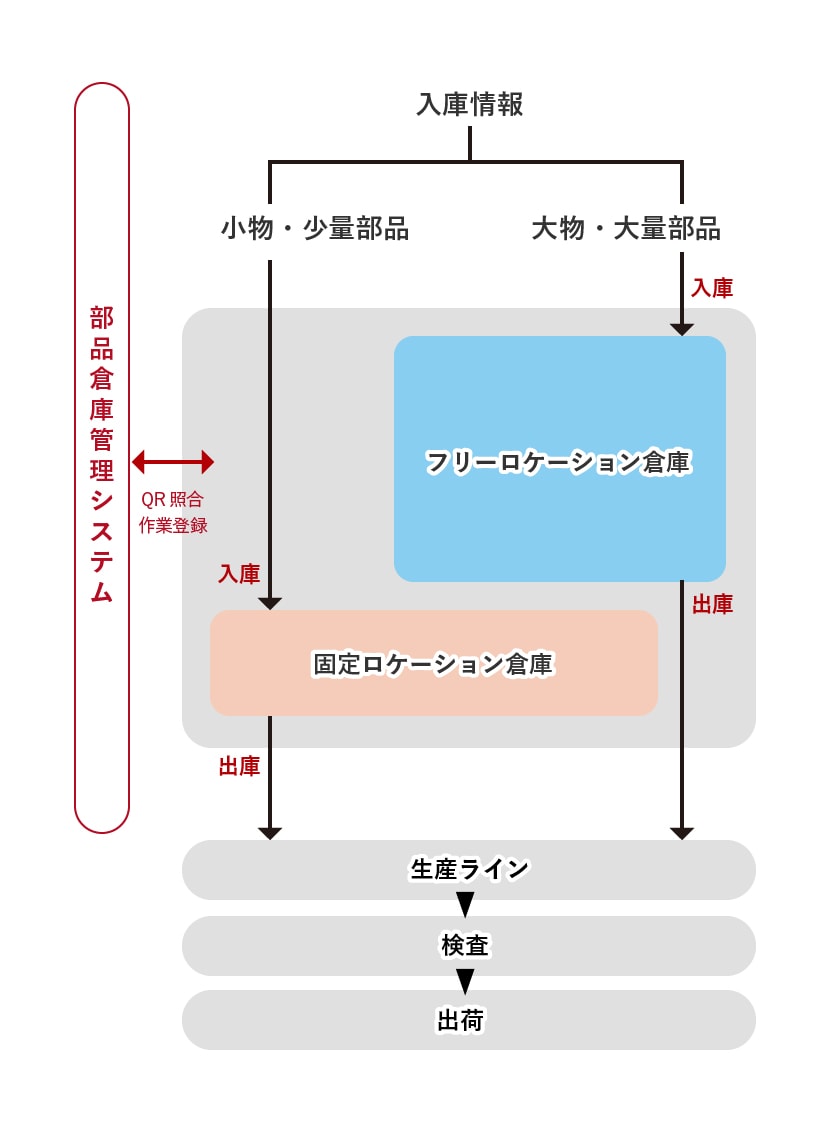